For Otago farmers Michelle and Rogan Borrie, a newly constructed feed pad on one of their three farms has been a game changer.
Cows are fed three to four kilograms of maize and grass silage on the feed pad and then sent to the milking shed.
Rogan points out that the simple design of the feed pad has fewer moving parts, and therefore fewer things to break down.
“There’s a scraper for the tractor and motorbike and a wheel pusher to push the silage in. The sharemilker’s got a silage wagon to feed the silage out.”
The feed pad project was taken on by NumatAGRI’s construction division.
“After talking to them, they were very keen to come on board and were very enthusiastic and wanted to come and build it for us,” says Michelle.
“So, we thought, well, why not? And we’re very happy with the results.”
She points out that NumatAGRI’s willingness to participate and dedication to the project was a driving force behind the successful implementation of the feed pad.
The Borries manage three farms in the Lower Waitaki Plains. Their operation features an expansive milking operation with about 2500 cows during winter. Recognising the need for change and the impact of weather on their farming practices, they decided to undertake an ambitious project – the construction of a new feed pad on a 500-cow dairy farm.
“Obviously things move forward and for environmental reasons we decided to put a feed pad on this 500-cow dairy farm,” Michelle says, emphasising their commitment to both animal welfare and environmental sustainability.
Their decision was precipitated by challenging winters characterised by heavy rainfall that turned the farm into a muddy mess, causing difficulty in pasture management and wastage of feed when feeding out in the paddock. In pursuit of a more effective and efficient system, the couple toured several farms to study existing off-paddock facility designs.
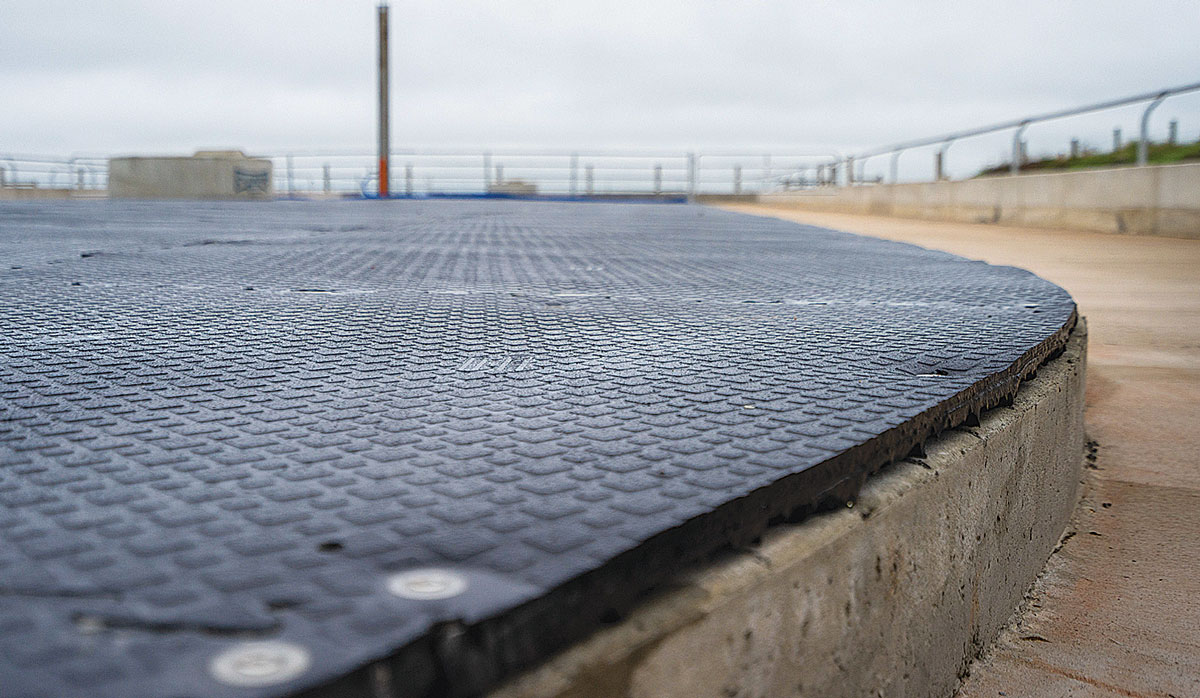 |
The rubber matting had a higher upfront cost but promised longevity and cost-effectiveness in the long run, the Borries say.
|
The Borries designed the feed pad following their explorative tours, identifying features they liked and aspects they wished to avoid in their design.
“We saw ones we liked, but a lot of them had woodchips, where we think woodchips are getting harder to get and dearer,” says Rogan, explaining their decision to opt for a rubber matting option instead. The rubber matting had a higher upfront cost but promised longevity and cost-effectiveness in the long run.
The rubber matting was also supplied by NumatAgri.
The project went ahead smoothly, seamless and with no unexpected hurdles, according to Michelle.
“I’ve worked with a lot of building agencies and stuff with lots of things happening on farm constantly. With Numat, this was just very smooth,” she says.
The couple is waiting to evaluate the full effectiveness of the feed pad design through a complete winter cycle.